Why Does Industry Struggle With HazCom Compliance?
Manufacturer's inability to communicate chemical hazards in the workplace remains a problem
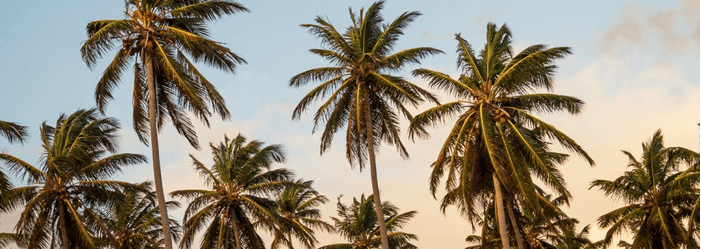
According to OSHA’s list of Top 10 Most Frequently Cited Standards for non-compliance, Hazard Communication ranked #2 with 2,682 violations reported across all industries. Non-compliance with hazard communication (HazCom) standards appears to be on the rise with figures showing a 38% increase in violations from 2021. OSHA data indicate that manufacturing sectors hold the largest share of the citations issued for non-compliance with HazCom. OSHA reports that the main reasons for industry non-compliance with the HazCom rule include:
- Lack of a written HazCom program that meets minimum requirements - 29 CFR 1910.1200(e)(1)
- Inadequate information and training on hazardous chemicals in the workplace - 29 CFR 1910.1200(h)(1);
- Absence of Safety Data Sheets (SDSs) in the workplace, or SDSs not readily accessible to workers - 29 CFR 1910.1200(g)(8); and
- Inadequate labeling of chemical containers in the workplace - 29 CFR 1910.120(f)(6).
We will always depend on manufacturers to safely develop, process, handle, and manage the chemicals which drive our economy and improve our quality of life. Of the more than 80,000 chemicals in common use today, many pose a serious risk of harm to health and safety from acute and chronic workplace exposures, and environmental release. The National Safety Council reported that in 2020, exposure to harmful substances or environments led to 424,360 non-fatal injuries and illnesses. In 2021, 798 fatalities were from chemical exposure were reported according to the Centers for Disease Control. There are monetary consequences also as industry pays out millions of dollars in OSHA assessed penalties each year just from non-compliance with HazCom standards.
For a long time, the ability of employers to effectively identify chemical hazards in the workplace and communicate those hazards to employees has presented problems for industry. OSHA’s HazCom regulations have a broad reach and ongoing compliance poses a critical housekeeping duty for industry. Consequently, HazCom is a “low-hanging fruit” for compliance auditors and workplace safety inspectors. From my years’ of experience with EHS compliance auding across a wide-range of industrial sectors, I’ve listed below the main challenges I see that prevent industry from achieving a winning HazCom program:
1. Management is genuinely unaware of the written HazCom program requirements and that several specific chemicals listed in 1910 Subpart Z have extra requirements for container labeling, workplace posting, and worker training;
2. Management’s inability to keep track of the numerous containers present in the workplace including the production floor, facilities maintenance shops, and on-site contractor areas;
3. Problems keeping chemical container labels affixed to certain types of containers, and the placing of labels on small-size containers.
4. Management assigns little time to maintaining its SDS list;
5. There are too few resources available to provide the appropriate level of HazCom training; and
6. Workers’ comprehension and retention of information relative to the Global Harmonization System for chemical labeling needs improvement.
Despite the cause, HazCom compliance deficiencies are easy to identify and many simple compliance assistance solutions are available. It is well worth a facility’s time to conduct routine in-house reviews of its HazCom program and workplace practices to assess compliance and fix issues before they result in an accident, injury, or inspection/audit finding.
OSHA’s full “Top 10 List” for 2022 can be found here https://www.osha.gov/top10citedstandards.